Almost the favorite section of "garage stories" - drivers' stories about how they managed to cheat the GLONASS system. Those who are older recall how they drained gasoline and fudged the mileage. Closer to the present day, it is more often a "technology" of draining fuel from the corporate tank into the personal tank.
But such situations will soon become a thing of the past, as modern transportation telematics systems are designed to "close the shop". Let's make it clear: the solution is not designed as a "tracking system", it is a technology for optimizing the work of special equipment: minimizing downtime, analyzing the work and preventing malfunctions
Is telematics something new or long familiar?
Telematics systems can hardly be called a market novelty. Today, such solutions are created by independent companies and manufacturers of special equipment, and some brands in recent years have installed such equipment on machines in the basic configuration. And, of course, consumers are familiar with such capabilities.
"Telematics systems for drilling operations have been actively used by mining companies around the world for more than 20 years. This includes Australia, North America and Europe," notes Pierre de Groulard, Export Director at LIM SAS.
"I will describe a solution for a fleet of 20-tonne trucks. A video terminal for controlling driver behavior monitors the condition of the employee and the traffic situation, helps not to be distracted. The video recorded in the terminal allows for a debriefing. Video segments in real time with indication of important moments are transmitted to the control room. The software allows you to build a "spider web" diagram for each driver to improve driving safety.
GLONASS terminal collects data on engine operation under load and idling, refueling and draining, fuel consumption. Fuel cards and controller of fuel accounting by RFID cards allows to build fuel balance without the participation of employees. This solution for a quarry with 20 dump trucks, four excavators and bulldozers, plus a mini gas station will cost about 5 million rubles".
Perhaps, in our country telematics systems do not fall under the category of must have yet. In any case, manufacturers of special equipment, whose machines are being equipped or are already equipped with this solution, say that the market is just getting acquainted with them and their capabilities.
"For equipment manufacturers, telematics systems as such are no longer a novelty. However, for many mining companies, the use of such solutions is still not quite familiar. Our dealers hold meetings with miners to tell them about the efficiency of telematics systems.
Given the fact that modern realities dictate their own rules of cost optimization, the management of enterprises has begun to pay much more attention to such solutions," says Dmitry Krasavin, Hitachi Construction Machinery Eurasia Technical Support Manager.
However, it is still necessary to agree on what is meant by such solutions and what capabilities should be considered new. Maxim Revyakin, Head of Galileosky's Sales Department, notes that telematics systems have existed as a phenomenon in production for a long time. But a few years ago, companies were more likely to buy solutions that today are seen as simple, i.e. devices that monitor only one parameter. The location of special equipment, for example.
"For the last 2-3 years, we have been approached with a large number of requests for the implementation of complex, integrated projects, where a large set of functions, flexibility and the ability to program the equipment are required. Now the devices help enterprises to monitor fuel level in the tank, tire pressure, position of the car in space (accident tracking), etc." says Mr. Revyakin.
Pierre de Groulard says that technology is constantly evolving and telematics systems are improving year after year. This is partly why they are still perceived as innovative.
"It's 2020. Quarries without telemetry collection look like endangered mammoths. Transportation monitoring is tightly integrated into the management processes of mining enterprises. Today, GLONASS monitoring technology provides not only positioning, but, together with a terminal for processing data from various sensors and dispatch software, represents a full-fledged business management center," says Dmitry Zhuravlevlev, Managing Partner of MONTRANS Group of Companies.
Monitors and analyzes
So, what can these systems do so well that without them, technology no longer looks modern? How can data on kilometers traveled, tons transported and liters of fuel used be converted into real money?
Dmitry Zhuravlevlev explains: the standards developed back in the last century have always contained a large reserve. In addition, everyone, from drivers to mechanics.
mechanics, were interested in averages.
Dmitry Zhuravlevlev explains: the standards developed back in the last century have always contained a large reserve. In addition, everyone, from drivers to mechanics.
mechanics, were interested in averages.
"But the world does not stand still. New technologies make it possible to operate machinery non-stop and achieve an operating ratio of 0.8 to 0.92" says a specialist from MONTRANS Group of Companies.
We have already mentioned that there is a sufficient variety of transportation telematics systems on the market today. In general, their tasks, functions and capabilities are similar, but not identical. Firstly, the solutions are installed on different types of vehicles. And secondly, each manufacturer and its dealers have their own distinctive features.
"These are just a few of the rig telematics system capabilities that have emerged in recent years.
• Drilling rig mast angle indicators that allow the rig to be positioned over the borehole with a high level of accuracy.
• Digital depth gauges that provide real-time data on the depth of penetration.
• Drilling parameter loggers that provide the acquisition, recording and transmission of this data at each depth mark. Drilling parameters include speed, tool pressure, torque, and fluid/air pressure, all of which allow the mechanical properties of the rock to be evaluated during drilling for hardness, heterogeneity, and fracture characteristics. The resulting charts allow blasters to determine and adjust the amount of explosives to be placed in the boreholes, which means not only savings in explosives, but also a more acceptable release during the blast.
• GNSS(GPS/GLONASS) positioning systems on the drilling rig that provide high accuracy navigation. Thanks to GPS/RTK technology, they help the drilling operator position the rig over the borehole to within a few centimeters.
• Machine monitoring systems (engine, hammer, etc.) using sensors mounted on the machine. Provide real-time information about the drilling machine status with sending notifications via sms or e-mail".
• Digital depth gauges that provide real-time data on the depth of penetration.
• Drilling parameter loggers that provide the acquisition, recording and transmission of this data at each depth mark. Drilling parameters include speed, tool pressure, torque, and fluid/air pressure, all of which allow the mechanical properties of the rock to be evaluated during drilling for hardness, heterogeneity, and fracture characteristics. The resulting charts allow blasters to determine and adjust the amount of explosives to be placed in the boreholes, which means not only savings in explosives, but also a more acceptable release during the blast.
• GNSS(GPS/GLONASS) positioning systems on the drilling rig that provide high accuracy navigation. Thanks to GPS/RTK technology, they help the drilling operator position the rig over the borehole to within a few centimeters.
• Machine monitoring systems (engine, hammer, etc.) using sensors mounted on the machine. Provide real-time information about the drilling machine status with sending notifications via sms or e-mail".
"Let me show you by example how it works. We have a map of our own design that shows all the machines equipped with JDLink. Here is a real grader in front of you, and here it is on the map. We specially generate an error: the current of the front headlights is lower than normal - and this information is immediately reflected on the screen of the monitoring center specialist. We have several such centers, each responsible for its own regions.
The information is transmitted to an employee in the relevant branch, who calls the customer, gives a transcript of the error and explains what it can lead to. This is proactive support: the owner of the machine may not even know that there is something wrong with his machine at that moment. We coordinate the service engineer's visit, and the service engineer already has a solution ready to fix the problem.
In this way we manage to prevent serious breakdowns, reduce the time for diagnostics and promptly eliminate the problem", - Ivan Komarov, specialist for after-sales technical support of Timbermash Baikal customers, described the capabilities of the system as a service tool.
The owner himself can also get information about the car by logging into his personal account.
"One of the useful functions of ConSite is control of unexpected breakdown of special equipment. When a machine alarm is triggered and a malfunction occurs that requires emergency intervention to avoid downtime, the system generates and sends an emergency report to the client.
It contains the location of the machine, the name of the fault, etc. At the same time with the owner of the machine, the report is also received by the dealer's employees, but with recommendations for troubleshooting," said Dmitry Krasavin about the similar capabilities of Hitachi telematics system.
"The main task of the My Sandvik system is to form a detailed picture of the processes occurring with machinery in the mines to make informed decisions. Thanks to their application, the productivity of the equipment fleet increases.
They can also improve mine safety by identifying operator misconduct, including speeding or driving in neutral. An important aspect is also the reduction of costs for unplanned repairs: telemetry identifies errors in control, which lead to the failure of components.
We are always ready to organize training of personnel to work with the system to improve the quality of equipment operation. The system analyzes fuel consumption, noting the time of idling. Subsequently, when adjustments are made to the operators' actions, it can be significantly reduced," said Oksana Gromova, Director of Marketing and Business Intelligence for the CIS, Sandvik Mining and Rock Technology.
This is what is meant by the phrase "optimizing machine operation". Several specialists spoke about the prospect of reducing operating costs by up to a third through the control and monitoring system.
"The task of telematics systems is not only to collect data on the location of machinery, its operating parameters and fuel consumption, but also to analyze the information obtained. In this regard, the ConSite service - a tool for monitoring, comparing and analyzing machine operation data - is easy to use.
Hitachi developers have introduced two main indicators: the non-operating time factor and the operating time factor of the excavator's turntable rotation operation. By obtaining these values, a fleet owner can quickly assess the efficiency of each machine," explains Dmitry Krasavin.
Ivan Komarov told stories from his practice. At the request of one of the company's clients, Timbermash Baikal employees analyzed the performance of the purchased machine. It turned out that the John Deere excavator worked about 7 motor-hours per day.
The owner is satisfied with this result, it seems that the machine is operated efficiently. But in JDLink you can see a more detailed picture: the machine dug for an hour and twenty minutes, moved for 30 minutes, combined functions for about 5 minutes. Total downtime was 5 hours, machine efficiency 25%.
The owner is satisfied with this result, it seems that the machine is operated efficiently. But in JDLink you can see a more detailed picture: the machine dug for an hour and twenty minutes, moved for 30 minutes, combined functions for about 5 minutes. Total downtime was 5 hours, machine efficiency 25%.
"There was a case when a customer came to us: he was trying to figure out what was causing the low productivity of the excavator. We looked into the system: out of 800 motor-hours, the hydraulics were only working for 300. It turned out that the problem was that there were not enough dump trucks for the quarry to work optimally. As a result, the company got two additional dump trucks," said a specialist of Timbermash Baikal.
"Telematics help to automate processes and reduce costs. For example, an enterprise engaged in geological exploration and oil production connected fuel level sensors to our devices to control consumption, refueling and prevent drains.
The dispatcher uploads data for a specific period and sees the time, place of refueling or unauthorized actions. The dispatcher easily compares actual fuel consumption with data from the driver. Such control has allowed the company to reduce significant financial resources during the working season.
After installing our devices, fuel expenses decreased by 30%, saving millions of rubles per month. In addition, the monitoring system was integrated with the 1C program. This helped to automate many processes in the company - from accounting to writing off spare parts, as the company's specialists receive real-time data on the parameters of equipment operation," Maxim Revyakin shared.
As for drilling rigs: here, too, optimization is possible through telematics systems, but their functions will be specific. The solution, for example, saves time when positioning the drilling machine boom over the borehole, assessing the quality of the passable massif and correcting the charging of boreholes with explosives.
In addition, the operator is able to rely on drilling parameters directly at the moment of operation and thus promptly correct his actions.
In addition, the operator is able to rely on drilling parameters directly at the moment of operation and thus promptly correct his actions.
"We worked at a site in Guinea, where the percentage of wells that met the customer's parameters (in terms of geolocation with an accuracy of 10 cm and depth) was as high as 64%. After the navigation system was installed, the number of such wells increased to 95%.
At the same time, the navigation system eliminated the need to physically mark the wells on the surface, well names were automatically displayed in the system, rig travel time was significantly reduced (with NaviLIM it took about 40 seconds to move the rig from one well to another), and the actual drilling plan was updated automatically based on the results of completed wells," said Pierre de Groulard.
Telematics systems and human factors
There is, however, a certain sensitive question: how do the operators feel about such innovations?
It is unlikely that an employee of a John Deere excavator, who actually worked 2 hours out of 7, would receive a bonus. And the employees of the oil production company described above were certainly not happy that they were caught draining fuel.
It is unlikely that an employee of a John Deere excavator, who actually worked 2 hours out of 7, would receive a bonus. And the employees of the oil production company described above were certainly not happy that they were caught draining fuel.
"Unfortunately, companies using telematics occasionally encounter sabotage by drivers. Most often it happens because of fuel consumption control - a dishonest employee loses additional and illegal income and tries to disable the device. The best way of protection is to place the devices in such a way that the driver does not have direct access to it," advises Maxim Revyakin.
"The owner of special equipment does not need to create a department to analyze the data received thanks to the telematics system. The ConSite service automatically generates monthly reports with information on the condition of each Hitachi machine in the fleet and recommendations for operation and sends them to the machine owner's e-mail.
In today's world, more and more attention is being paid to automating processes using telematics systems. Hitachi also contributes to the development of this area, working on the task of reducing machine downtime.
In the past, it was the responsibility of plant mechanics to schedule maintenance on time, but now ConSite's automated service is helping them to do so. "We have been using and testing automation, monitoring and telemetry systems for mining equipment for quite some time, offering a choice of software packages to improve safety and productivity in mining operations.
The My Sandvik system, which automatically collects, transmits and processes information about the operation of self-propelled mining equipment, is already in active use in CIS countries."
In today's world, more and more attention is being paid to automating processes using telematics systems. Hitachi also contributes to the development of this area, working on the task of reducing machine downtime.
In the past, it was the responsibility of plant mechanics to schedule maintenance on time, but now ConSite's automated service is helping them to do so. "We have been using and testing automation, monitoring and telemetry systems for mining equipment for quite some time, offering a choice of software packages to improve safety and productivity in mining operations.
The My Sandvik system, which automatically collects, transmits and processes information about the operation of self-propelled mining equipment, is already in active use in CIS countries."
However, almost all of our experts are optimistic - they say that the cautious attitude is present only at first, and then either successful practice or training events help.
"Most likely, when drilling operators start working with such equipment, they will be wary of it, because it is designed to control their work in one way or another. However, over time they usually come to realize that such solutions significantly increase drilling productivity, and with the right company policy, the time savings and improved comfort level of working conditions motivate personnel to adopt new technologies" Pierre de Groulard believes.
"We have been applying and testing automation, monitoring and telemetry systems for mining equipment for quite some time, offering a choice of different software packages to improve the safety and productivity of mining operations. The My Sandvik system, which automatically collects, transmits and processes information on the operation of self-propelled mining equipment, is already in active use in CIS countries."
"It happens that operators unfamiliar with the ConSite service perceive it as a system of tracking their work and fear that the owner may see violations of the rules of equipment operation. The developers of this tool did not set the main goal to monitor the actions of operators and shift all responsibility for the effective use of equipment to them.
"It happens that operators unfamiliar with the ConSite service perceive it as a system of tracking their work and fear that the owner may see violations of the rules of equipment operation. The developers of this tool did not set the main goal to monitor the actions of operators and shift all responsibility for the effective use of equipment to them.
The purpose of this service is to advise everyone involved in the process on how to operate the machines correctly in certain modes that correspond to the conditions of the work site, and to prevent breakdowns and subsequent costly repairs" explains Dmitry Krasavin.
"The human factor is a very common problem. However, we position our system as a diagnostic tool to manage and adjust production processes and improve the availability of the equipment fleet. Having obtained data on machine operation, we can conduct training seminars for employees of the mining enterprise and reduce the influence of human factor on the technical condition of the equipment," emphasizes Oksana Gromova.
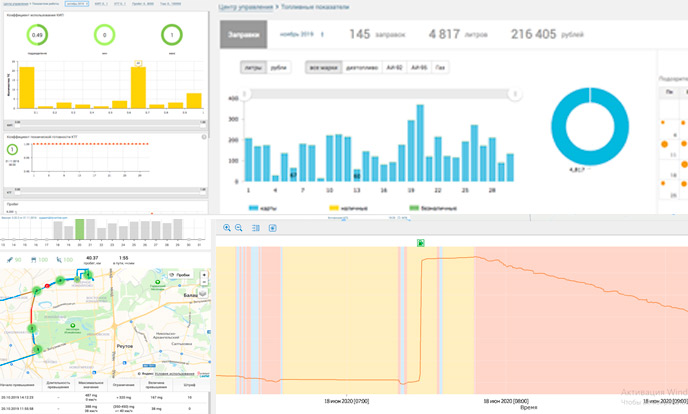
In turn, MONTRANS has developed an innovative product in the field of transportation monitoring and fleet management - MONTRANS Analytics
This system significantly expands the possibilities of telematics, combines many parameters and automates the process of fleet management
This system significantly expands the possibilities of telematics, combines many parameters and automates the process of fleet management