Properly organized vehicle operations are half of a company's success, no matter what industry it operates in. Disruption of logistical processes and interruptions in the movement of vehicles can de-energize a company and even lead to the closure of the business.
The digitalization of a company helps to avoid many risks, visualizes processes and sets the trend for profit. According to the Institute for Statistical Research and Knowledge Economy at the National Research University Higher School of Economics, the demand for cloud technologies in the transportation industry in Russia is increasing by 21% annually. By 2030, scientists predict a complete transformation of logistics, which will unite aviation, road, rail, sea and river transportation into a single ecosystem. But in order to bring the beautiful future closer to their garage, owners of even small depots need to start by analyzing the efficiency of their vehicles and installing or fine-tuning satellite transportation monitoring systems. The practice of recent years shows that it is problematic for most transport companies to start digitalization. There may be several reasons for this: corporate bureaucracy, the need for coordination between departments, difficult access to 1C, and fears of breaking processes built up over the years.
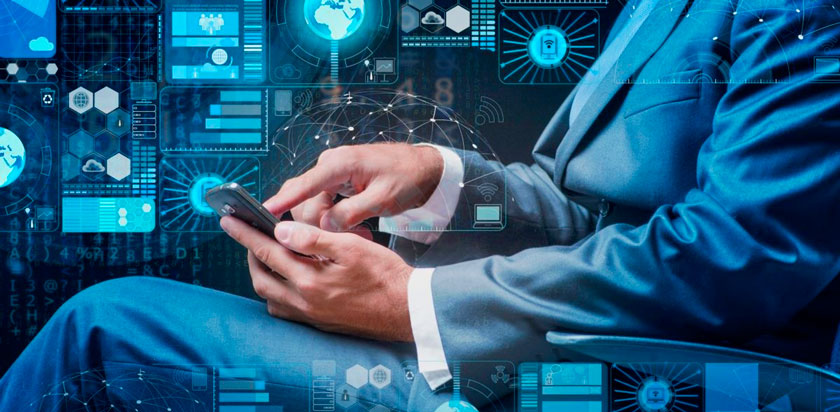
Meanwhile, fleet business automation is solving problems:
- reducing fuel and lubricant costs
- Optimization of vehicle maintenance costs
- Increasing vehicle utilization rate
- Budget savings for the purchase of new equipment
- ensuring transparency of document flow
- increased transportation safety
- increasing the speed of data processing and reducing the time for decision-making
- creation of a unified information platform for all transport company divisions
- possibility of long-term business planning
- Optimization of vehicle maintenance costs
- Increasing vehicle utilization rate
- Budget savings for the purchase of new equipment
- ensuring transparency of document flow
- increased transportation safety
- increasing the speed of data processing and reducing the time for decision-making
- creation of a unified information platform for all transport company divisions
- possibility of long-term business planning
The first stage of digitalization, which all companies go through, is equipping vehicles with GPS-monitoring elements. Fuel level sensors and satellite navigation terminals relieve the owner of the enterprise of many pains. The main expenses in ATP come to fuel, repair and operation of equipment and salaries of employees.
After installation of telematics we get:
- drivers stop draining fuel
- movement of fuel and lubricants throughout the enterprise becomes visible and transparent
- Vehicle location is under control in 24/7 mode
- idle time, useful work and idling are visible
- driving becomes safer
- Reduces the number of employees controlling the operation of vehicles
- movement of fuel and lubricants throughout the enterprise becomes visible and transparent
- Vehicle location is under control in 24/7 mode
- idle time, useful work and idling are visible
- driving becomes safer
- Reduces the number of employees controlling the operation of vehicles
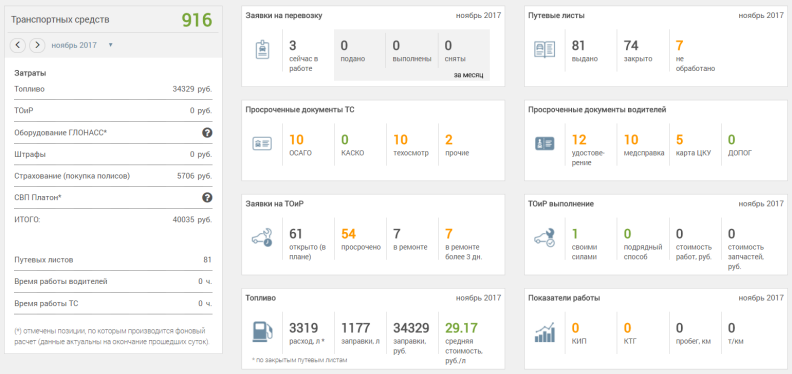
Once the telematics system is up and running, and millions of different metrics are uploaded to a cloud service, management is faced with the following question: what to do with this large amount of data (Big Data)? To process, analyze and draw conclusions about the performance of the technology will require a huge staff of specialists. And here comes the second stage of digitalization of the depot, when processing and analytics of big data is entrusted to software services. For example, MONTRANS.ONLINE is a development of domestic programmers, which is a complex management system for a motor transport enterprise. The analogs in the world practice are called Fleet Management Systems (FMS). The main advantage of this solution is the integration of transportation monitoring data with the functions of its control and management. Fleet managers do not need to work with several programs and spend time on data exchange between them. MONTRANS.ONLINE manages the fleet in “one window” mode, when digital, quantitative, qualitative, percentage characteristics of various parameters are collected on a single display.
Sergey Kulakov, Commercial Director of MONTRANS Group of Companies: “MONTRANS.ONLINE solution can be called ‘Flight Control Center’. The service tracks the location of vehicles online 24/7. Controls the speed of vehicles, fuel consumption, refueling, drains, GLONASS on-board equipment readings. Shows the actual consumed resource of equipment, schedules maintenance and repairs. Keeps a unique transportation card for each vehicle. This passport contains technical characteristics, a photo of the vehicle, installed sensors and terminals, valid insurance policies, completed inspections and repairs, fuel consumption rates. In addition, the program tracks the driving style of each employee and creates driver ratings. These are: speeding, sudden acceleration and braking, facts of traffic violations, insurance payments in cases of traffic accidents, control of labor and rest regime. In logistics firms, the software records the receipt, creation and execution of requests for transportation services, cargo and passenger transportation. The platform generates work schedules for each unit of equipment with subsequent assignment to a route and control of its fulfillment. Remote medical pre-trip medical examination and MONTRANS DVR driver monitoring and assistance system can be connected to this application. This is one of the latest developments in road safety and transportation. Our experience has shown that the IT solution reduces the probability of accidents by 80%. And this means saved lives of employees and significant budget savings on repair and restoration of equipment”.
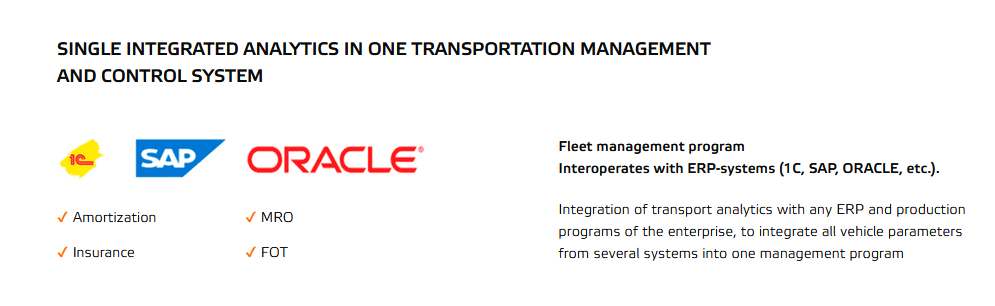
Reports on monitoring, operation, performance and maintenance of vehicles are saved in any existing formats. The data are uploaded to 1C, SAP and other similar accounting mechanisms of the auto enterprise and are used by fleet management to manage the auto enterprise. But Russian IT specialists have developed another program, which is designed for business owners themselves. MONTRANS.ANALYTICS cloud service fundamentally changes the management system of a motor transport organization. The owner is rid of viewing a lot of charts, tables and diagrams. The manager receives top-level reports with key fleet performance indicators. The information is presented in an accessible form, understandable and does not cause doubts in reliability, as the human factor was excluded during its preparation. The first person of the corporation will be able to see at once - where the business is “down”, and where the production is going uphill. It remains only to draw conclusions and make the only right decision.
MONTRANS.ANALYTICS simplifies the tasks of technical and financial administration by combining all indicators in a single management standard. The program controls costs, helps to reduce costs, and shows directions for increasing the company's profit. For example, in 2020-21, such large companies as:
MONTRANS.ANALYTICS simplifies the tasks of technical and financial administration by combining all indicators in a single management standard. The program controls costs, helps to reduce costs, and shows directions for increasing the company's profit. For example, in 2020-21, such large companies as:
- NOVA JSC's corporate telematics platform (Construction and field development, more than 1,500 vehicles);
- NOC LLC fleet analytics project (Mining, over 600 vehicles, 12 subsidiaries);
- Korpanga Severstal LLC fleet digitalization project (Mining, over 100 vehicles);
- Ecolife LLC vehicle fleet digitalization project (Solid Waste Management, over 500 vehicles);
- Vehicle monitoring system of GAZSTROIPROM PJSC (more than 8,000 vehicles).
- NOC LLC fleet analytics project (Mining, over 600 vehicles, 12 subsidiaries);
- Korpanga Severstal LLC fleet digitalization project (Mining, over 100 vehicles);
- Ecolife LLC vehicle fleet digitalization project (Solid Waste Management, over 500 vehicles);
- Vehicle monitoring system of GAZSTROIPROM PJSC (more than 8,000 vehicles).
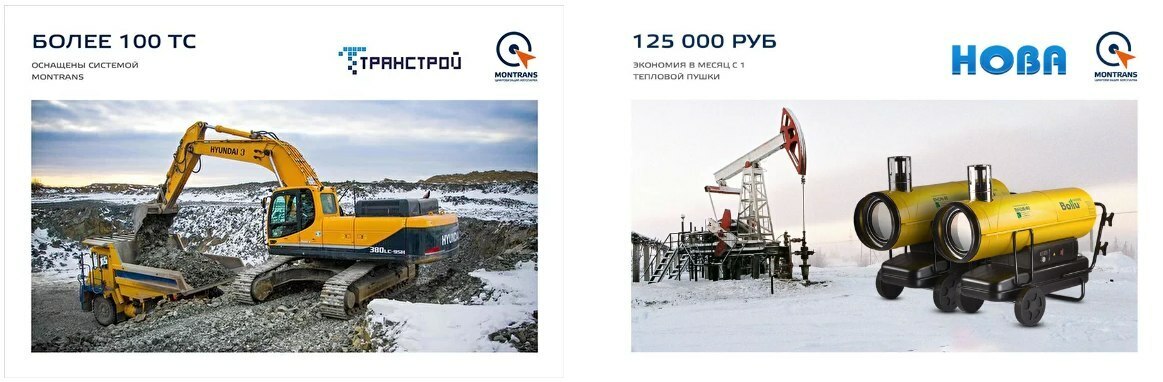
Experts of the IT research consulting company Gartner have calculated that by the end of 2023, transport organizations that neglect digital technologies will increase their costs by 25% and time costs by 15%. As the experience of the MONTRANS Group of Companies shows, investments in the digitalization of institutions pay off in 4-6 months. Moreover, for companies that want to improve the efficiency of their departments, there is no need to create their own servers. “MONTRANS” offers a ready-made solution, ensuring the correct operation of IT-systems, on which the fleet business is already functioning.